DR10 Thermal Oxidation Testing
DR10
ITR Tube Deposit Rater Instrument (Thermal Oxidation Stability of Aviation Turbine Fuels) - Aviation Turbine Fuel
ASTM D3241
ASTM D1655
ASTM D7566
ISO 6249
Def Stan 91-9
Summary
Thermal Oxidation Stability of Aviation Turbine Fuels, ASTM D3241 is universally used by the industry to measure high temperature stability of aviation turbine fuels. The ASTM D3241 is required to be run on every batch of jet fuel produced according to ASTM D1655 or DEF STAN 91-91 specifications. In this test method, the fuel is pumped through heater tube at fixed flow rate and during a specified period of time. The fuel is pass or fail rated according to the amount of deposit formed on the heater tube at a specified temperature. Traditionally, the amount of deposit on the tube is rated visually against a reference color scale. The proper rating requires significant experience and expertise. However, operator capabilities vary, so evaluation of color can be quite subjective.
Many articles have been published on the fact that color does not provide real information on the thickness and volume of deposits, parameters which are far more meaningful for characterizing jet fuels for users and suppliers. The aviation fuel industry found that one of the most crucial stages of this test method is an objective analysis of deposit produced on the heater tube.
New! Innovative DR10 Instrument
A new instrumental method of quantitative measurement of tube deposits has been developed by AD Systems, in which the thickness of the deposit is accurately determined by an automatic instrument, reducing test subjectivity. The innovative DR10 instrument uses an interferometry technique (ITR) for precise measurement of deposit thickness in nanometers. This stand-alone compact instrument can be easily installed in any location in minutes. The operation is based on a powerful light source, a spectrometer with fiber optic probe and specially designed application software.
The DR10 test is simple and straightforward. The heater tube is prepared according to ASTM D3241 test procedure and is then placed in the test chamber of the DR10. Using an intuitive graphical interface with touch screen panel, the operator enters sample information and starts a tube scan. Specific light is emitted and directed onto the surface of the heater tube. The reflected light is collected and the interference created by the deposit is monitored by the spectrometer. The software analyzes the interference and calculates the deposit thickness. Precise thickness measurements are taken at 1,200 points along and around the tube surface. A detailed test report is ready in less than 15 minutes.
The DR10 test report provides a 3-D profile of the deposit distribution on the tube surface. The software automaticaly detects and reports the Standard Spot value which is the mean deposit thickness of the thickest 2.5 mm2 area as defined in ASTM D3241. The average and the maximum thickness deposit values, as well as the calculated total deposit volume are reported. For complete test traceability, the DR10 report is tagged with the heater tube serial number picture taken by the built-in camera.
Methods
ASTM D3241, IP 323, ISO 6249Aviation Turbine Fuel - Standard Specification ASTM D1655 and Def Stan 91-91
The test results are indicative of fuel performance during gas turbine operation and can be used to assess the level of deposits that form when liquid fuel contacts a heated surface that is at a specified temperature.
The DR10 ITR - Tube Deposit Rater is now part of ASTM D3241-14B, Annex 2. Annex 2 provides for the use of the ITR technique (Interferometry Tube Rating) which is the technique used by the DR10.
ASTM Sub Committee D02.0J, which is responsible for jet fuel specifications (ASTM D1655 and D7566), updated ASTM D1655 and D7566 to include pass/fail limits for the Thermal Oxidation Stability of Aviation Turbine Fuels test in as follows:
In addition to the "3 color code and the no peacock or abnormal deposit", an 85 nm maximum deposit thickness will be noted with a new note K. Note K will be as follows: "The ITR and the ETR techniques are the preferred techniques to evaluate the Jet Fuel Thermal Oxidation deposit."
This implies that the ITR in Annex 2 becomes a primary or "referee" technique to the VTR visual tube rating technique.
Application
The DR 10 is designed for all types of applications related to thermal oxidation testing of aviation turbine fuels including research, refining, pipeline, terminals, and mobile laboratory applications - every location where thermal oxidation of jet fuel is evaluated.
Benefits
- Absolute measurement of deposit thickness
- Quick, accurate and objective rating
- Push of a button operation
- Very compact design
- Rigid construction
Operation
The operation is based on a powerful light source, a spectrometer with fiber optic probe and specially designed application software.
The reflected light is collected and interference created by the deposit is processed by the spectrometer. The software analyzes the interference fringes and calculates the deposit thickness. The full scan of tube surface on 1,200 points is completed in less than 15 minutes.
- The heater tube is prepared according to ASTM D3241 test procedure and is then placed in the chamber of the DR10 Deposit Rater.
- The tube is then placed in the Test chamber of the DR10.
- All samples details are entered and the operator presses the START button.
- The result is reported after 15 minutes.
Reporting
At the end of the test, the result in saved in a built-in data base that can contain up to 100 000 results. The thickness deposit is reported in nanometers. The 3D deposit profile is displayed on the screen, any deposit thickness area greater than 85 nm is displayed in red color. The results can be displayed, printed, memorized on a USB disk on key or send to a LIMS via the LAN connection.
The DR 10 reports the following data:
The Standard Spot Thickness
The DR 10 measures the deposit thickness at 1200 different points of the heater tube circumference. The standard spot thickness is the mean thickness deposit for the six thickest points in a 2.5 mm2 area (according to ASTM D3241 method definition). Grid of 50 x 24 Points
The deposit volume
The deposit volume is the total deposit volume measured on the circumference of the tube on a length of 50 mm.
Maximum thickness
The maximum deposit thickness is the thickest point among the 1200 measured points
Average thickness
The average deposit thickness is the mean value of the 1200 measured points.
List of parameters saved with a result:
- Sample Type
- Sample ID
- Date and Time
- Operator name
- Test Rig Identification used for the Thermal Oxidation Stability of Aviation Turbine Fuels
- Thermal Oxidation Stability of Aviation Turbine Fuels temperature
- Heater tube serial number
- Comments
- X and Y Coordinates for the standard spot localization
- Calibration information (tube serial number + date of calibration)
- Instrument serial number
- Software version
DR10
For more information on this product or to arrange a call from one of the Cea Petrochemical Team, please complete the contact form below.
SUBMIT
Name:
This field is required.
Email:
This field is required.
Phone:
This field is required.
Industry:
This field is required.
Company Name:
This field is required.
Address:
This field is required.
Post Code:
Country:
This fi.
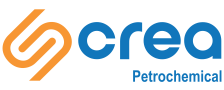