NEW ONLINE 700
ASTM D5191
Automatic process analyser - CE marked
Subject
Determination of Air Satured Vapour Pressure on gasolines, completely on line, full automatically, extremely accurately and fast with the New-on-line 700.
The New-on-line 700, making part of the new generation of on-line process analysers, determines Air Satured Vapour Pressure in correlation to the norms, while guaranteeing:
Perennity: conceived in order to have a raised longevity thanks to the good quality of the mechanical, electric and electronic components used for its manufacturing.
Simplicity: a modular architecture of design.
Supervision: accessible by Ethernet network on site or by safe remotely connection made by Internet
Access for user and/or manufacturer
Conviviality: with a clear and didactic graphic interface.
This design brings a maintainability never reached on these analysers and in particular on the ASVP Analysers which don’t require a particular maintenance. New-on-line 700 determines the Air Satured Vapour Pressure in correlation to the ASTM, IP, ISO, DIN standards by using technologies of on-line processes. With a reduced time of analysis (3 – 6 minutes) it allows a constant control in real time of the lines of production. The management of the analyser is completely automatic thanks to the dedicated software which allows the user to supervise and visualize all the parameters referred to the analysis in progress.
Determination of Air Satured Vapour Pressure is made by a precision pressure sensor that measure constantly the absolute value during the test. The analyser, by means of the Lin–Tech software, observes and manages the phenomenon. As soon as the result is obtained, the cell is emptied automatically and a new cycle of analysis starts.
Generality
This analyser consists a pressurised enclosure, EEx p for zone 1 and 2, with a CENELEC, ATEX certification and different accessories fixed on both sides of the enclosure.
The protecting system and some EEx d boxes are fixed on the left side, and the analytical part fixed on the right side.
In the upper part of the enclosure accessible with a door supporting a flat screen, are enclosed, the PC, the electronic, the interfaces and the interlock with the terminals.
This analyser is supplied with some components for the sample conditioning procedure. In option, a complete sampling conditioning system dedicated to a user application can be supplied.This analyser has been designed to follow the reference standards methods.
The analytical cell is cooled down with Peltier elements.
This type of analyser has a main application in production unit where the sample composition does not change rapidly in a short period of time.
Principle of Detection
A chamber of 15 ml is maintained at 0.1 kPa and 37.8°C.
A quantity of 3 ml of sample, with a temperature of 0 °C, after the air saturation procedure, is automatically injected by means of a pneumatic injector inside the cell of 15 ml.
Due to the temperature a certain volume of sample changes from the liquid phase to the gas phase.
This mutation modifies the absolute pressure inside the chamber.
When the stabilisation of the pressure is reached, the volume of the absolute pressure obtained will be considered as the total vapour pressure.
Procedure of Analysis
The application software proceeds to the draining first, by flushing the sample to the drain.
This operation takes a few seconds.
The second step is to fill the test tube on a time basis.
When the time of filling is elapsed, a seconde draining procedure can be done if necessary.
Then the analysis is started.
All this procedure of draining and filing takes 5 to 20 seconds depending on the selection made in the set-up software.
The analysis time will takes 3 minutes up to 6 minutes.
The user can select the mode of analysis and also can do alternatively both methods.
The analyser can select a reference sample from one external drum to proceed to the validation of the analyser himself, before to start the analysis on the product line.This type of analyser is specially designed for production unit where the results have to has close as possible of the ASTM reference result from the laboratory.
Measuring Parameter
Air Satured Vapour Pressure on gasolines according to the standards reference methods
Temperature in degree Celsius
Measuring span –60°C to +60°C
Sample Characteristic
Input analyser
flow 10 to 20 l/h (in drain status)
consumption 2 … 4 l/h (according number of analysis)
pressure 0,3 – 0,8 bar
temperature maximum + 40 °C
contamination without solid particle > 10 microns
without presence of acid or solvent
maximum 100 ppm water
without traces of residue
Sampling conditioning items
1 ball valve stainless steel 316L sample input
1 filter 10 micron
1 rotameter stainless steel/glass 0-40 l/h with low flow alarm (contact NO/NC on terminal of the analyser)
1 three ways solenoid valve
1 ball valve stainless steel 316L reference sample input
Output analyser
As to be connected to a purge collector supplied by user
Specification ‘s purge collector
atmospheric drain
without back pressure
The purge collector has to be always below the level of the output of the analyser (gravity flow)
Options: sampling conditioning system
4 ball valves
filter in line
water heat exchanger
2 rotameters
1 solenoid three ways valve for sample reference input
pressure reducer
Utilities
Air supply (shut-off valve supply by the user):
without oil and dust
dew point max –20°C
pressure 4 to 7 bars
consumption about 30 Nm³/h
Water (shut-off valve supply by the user):
clean without sludge or particles
input pressure min 1 bars, max 3 bars
differential pressure input/output min 1 bars
temperature max +15°C
consumption max 300 l/h
Power supply
220V / 5% / 50Hz / 2 KVA
380V / 5% / 50Hz / 1,5 KVA three-phase
Control Unit
The control unit assembly is mounted internally into the pressurised enclosure. This assembly include:
Panel PC working on Window® based application
Interface boards, input/output digital and analogic
Power supply DC
Light boards IR
Interface
Input/output modules, with galvanic separation
Local Display
Flat screen (15’/17’) touch screen and/or 4 buttons for control functions connected by the panel PC.
Informations Displayed
Record of all the critical parameter‘s display of the last 30 results from the application software
Alarm with description of the default
Access to all the function‘s
No programation required
All results stored on hard disk
Software
Used with the 4 push buttons front door mounted
ASVP applications
Set up software (purge time, drain time, 4 to 20 mA range, record span etc.)
Calibration software
Maintenance software
Analytical Cell
The analytical cell is mounted externally on the pressurised enclosure
The cell is cooled by Peltier element
Analysis cycle time is 4 to 6 minutes
Repeatability
5 mBa
Resolution
1 mBa
Internal Security
Watch-dog
By PC or interlock watch-dog default, the watch dog turn off the electrical power of all the components except the PC
Alarm Output
Default analyser: 1 contact
Low sample flow: 1 contact
Low water flow: 1 contact
Input Signal
1 Contact, stand by, analysis cycle interrupted
1 Contact, start analysis, restart of an analysis cycle
Output Signal
4 to 20 mA accessible from the set-up linear module, galvanic separation, max load 600 Ohms
Cooling Devices
Water cooled of the hot side of the Peltier element
Lowest cell temperature –35°C (with cooling water at +10°C)
Ambient Conditions
Temperature + 5°C to + 40°C
HR 80% maximum
No excess of dust or corrosive atmosphere
Installation: analyser house or shelter
Radio Electric Perturbation
For all the standard frequencies don’t use radio at less than one meter ot the analyser
Classification
Classification EEx p II B T 6 / according CENELEC 50016
Option : EE × P II C T6
Fittings
Input/output sampling tubing 4/6 mm
Air supply ¼ and ¾” NPT female
Gland PG 13 or PG 16
Enclosure
Class IP 65
Special Options
Serial line RS 422 Modbus protocol
Calibration decade box, ISO 9002 for PT 100 (supplied with connectors)
Reference sample for validation of the analyser
Sampling conditioning system, according application
Procedure of Control Before Dispatch
Electronic calibration
Analytical calibration on reference certified samples
Control of functionality on certified sample in sample loop with about 100 results
Certificate supplied on the status of calibration and tests done
Usefulness
The instrument is equipped with Peltier elements
The cooling water can be supplied by an already existing water line or by external chillers (option available upon request)
Sample conditioning at 0°C
Pneumatic injector of 3 ml sample quantity
Measuring cell at 37.8 °C with pressure sensor
Loading valve, draining valve and sample depressurization in bottle
Vacuum pump
Control system for pneumatic valves and pressure regulator
PT100 temperature probe for conditioning and measuring cell
Characteristics of the Sample
Flow: 10…30 l/h in rinsing phase
Consumption: 2 … 5 l/h, depending on analysis numbers
Pressure: Min 0,3 bar / Max 0,8 bar
Contamination
Without solid particles > 10 microns
Without acid and solvent presence
Max 100 ppm of water
Inlet temperature
Max 35 °C
Min +10°C above the higher Pour Point result
Alternative Products
A sentence here about related products with image links below to products you want customer to consider.
SUBMIT
Name:
This field is required.
Email:
This field is required.
Phone:
This field is required.
Industry:
This field is required.
Company Name:
This field is required.
Address:
This field is required.
Post Code:
Country:
This fi.
New Online 700 Air Satured Vapour Pressure
For more information on this product or to arrange a call from one of the Cea Petrochemical Team, please complete the contact form below.
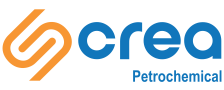