NewLab 200 Cold Filter Plugging Point
Standards
ASTM D6371, IP 309, IP 419, EN 116, EN 16329
CE marked
Subject
Cold Filter Plugging Point of diesel, biodiesel and heating fuels.
Measuring CFPP Principle
The sample is cooled down according to the methods and when the preselected temperature is reached a vacuum of 20 mBar is automatically applied to the sample. The product is sucked through the filter into the calibrated aspiration pipette. If the sample takes more than 60 seconds to reach the upper barrier detector (during the aspiration phase), or it fails to return completely into the test jar before that the product has cooled by a further 1°C, the Cold Filter Plugging Point is reached.
Measuring CFPP Devices
Aspiration pipette
Filter assembly
Light barrier
Measuring Temperature Probe
Platinum resistance PT100 class A
Accessories
OilLab 250 – external vacuum generator including:
Vacuum pump
Two glass bottles
A glass cork with: u-tube, funnel, manual flow regulating valve
OilLab 255 – internal vacuum generator including:
1 x micro-pump of 350 mBar
1 x electronic pressure / vacuum regulator composed by: proportional valve, pressure / vacuum control sensor, regulator for reference vacuum generation at 20 mBar, vacuum stabilizer
Measuring Parameters
Temperatures: in °C
Measuring range: +80°C … -80°C
Resolution: 0.06 °C
Accuracy: ± 0.1 °C
Repeatability / Reproducibility: as per standards methods or better
Software Features
New LabLink software able to manage up to 6 analytical heads simultaneously (stand alone)
User friendly interface
All analytical parameters recorded
Customizable analysis parameters and methods
Customizable results report
Printable graphs and results
Self-identification of the typology of the analysers connected
The software includes:
Analysis Menu
Standard method as per ASTM / IP / ISO / EN / DIN… norms of reference
Optional methods:
T-sample – T-bath (Delta T constant)
cooling rate °C / h
selectable bath steps
fast bath with selectable temperature
Audible alarm and displayed messages at the end of the analysis and in case of errors and/or malfunctions
The parameters displayed and updated in real time are:
sample temperature
bath temperature
vacuum pressure
low level light value
up level light value
aspiration time
release time
intertime test
Thanks to an istogram (graph) that shows the aspiration and release times it is possible to observe the behaviour of the sample during its cooling phase
This feature is an excellent tools for the observation and evaluation of the additivations actions and behaviour
Diagnostic Menu
Direct access to all analog, digital, inputs and outputs
Selectable value displaying: °C / Volt
Vacuum data displayed in mBars
Calibration Menu
Automatic calibration of each temperature probe
Automatic calibration of vacuum sensor
Last calibration date referred to each single probe displayed and relative data printable
Display of calibration diagram
Insertion of offset values
Standard and advanced calibration modes
Data Utilities
Fields for introduction of operator and product name
Archive viewer for files recall
All analysis stored in Excel® compatible format
Storage capacity for more than 60’000 analysis
LIMS compatible
Integrated Touch Screen Panel PC
TFT/LCD 12"
Resolution 1024 × 768, 16.2 M colours
2 USB ports for connection to an external printer and/or external PC
Storage capacity for more than 60'000 analysis
Cleaning pipette procedure
By using a suitable cleaning liquid and pressing the relevant function button the analyser performs a cleaning sequence of 10 aspirations cyclesEasy removing of aspiration pipette and filter assembly allows cleaning according to the methods
Test Jar
Same dimensions and volume as described by the standard test methods
Product level mark
Small edge on the top in order to fix the glass cell to the analytical head
Cooling System
Integrated gas CFC free motor compressors:
Single stage (for temperatures up to -40°C / 1)
Double stage (for temperatures up to -80°C / 2)
Equipped with an automatic energy power save system. After 15 minutes from the end of the analysis the cooling system goes in stand-by mode.
Safety Devices
Pressure controller for 1st stage motor compressor
Pressure controller for 2nd stage motor compressor
Thermostat for 2nd stage activation
Thermo-switch for each cooling / heating jacket
Motor compressors equipped with internal overload devices
Electrical Supply
220V ± 15% / 50 to 60 Hz
115V ± 15% / 60 Hz
Cord Cable
3 conductors flexible cable 2 m (7 feet) length with PVC sheath oil and heat resistant as per CENELEC directives
Ambient Temperature
Max 32 °C
H.R. 80%
Alternative Products
A sentence here about related products with image links below to products you want customer to consider.
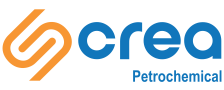